Chemicals
ERP Software for Chemical Industry
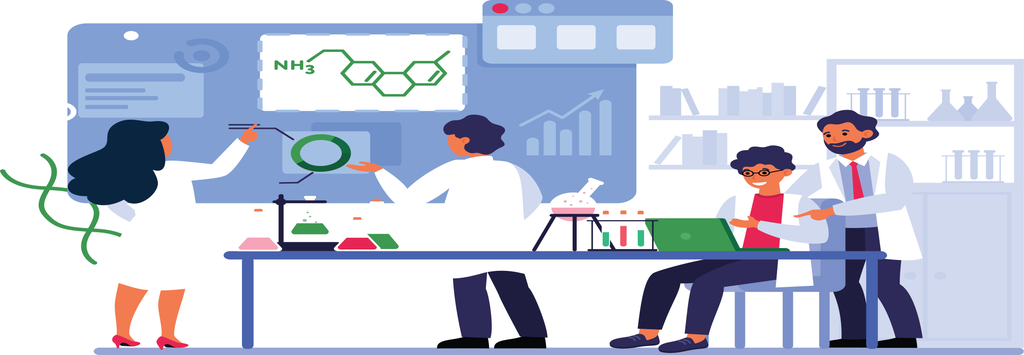
Chemical companies have to work within a very strict business environment and ecological laws while investing immensely in environmental engineering, waste disposal management, fire hazards and industrial safety standards. Moreover there is stiff global competition for large manufacturers. Companies need to get the best out of their processes with the least investment to maintain profitability and market share. To achieve these objectives, many chemical companies implement ERP Software for Chemical Industry which integrates and automates their processes thus reducing the cost and increasing the efficiency manifold. The problems faced by chemical companies are similar to any other process manufacturers but in addition to that chemical manufacturers have some unique requirements that can only be met by specialized ERP for Chemical industry.
Regulatory Compliance (MSDS, etc.), Co-Products, By-Products & Recycling, Special Characters Support, Active Formula Adjustment, Reformulation, Research and Development, Lot History, Shelf Life, Multiple Units of Measurement are some of the unique requirments specific to chemical industries.ERPNext software for Chemical Industry is an extremely evolved and mature ERP System that has been recognized for being extremely effective for the erp software for chemicals industry.
Critical Features of ERP System for Chemical Manufacturing Industry
Quality Assurance
Flexible creation of QC parameters for raw materials, WIP, SF Goods and Finished Goods, with possibility of defining upper/lower limits of any spec. and flagging for a mandatory parameter that may result in stopping a batch based on that critical spec. Pre-process, in-process and post-process Quality Control Testing. Possibility of manual entry or interface with lab equipment. Printing of QC Analysis Reports in required formats of different statutory authorities. Upload or attaching of independent third party lab reports with an item or product for submission at a relevant stage. Attaching or embedding SOPs for different processes for cGMP support. Availability of analytical reports to cater to different needs. Full regulatory support including EC Numbers (EINECS/ELINCS), MSDS Printing, etc. SARA, Bioterrorism Act and other regulatory reporting, as well as support for in-house EHS programs.
Sales-Marketing
Pricing, Category based Specific pricing, Advanced Forecasting, with transfer of forecasts to Sales Orders. Sales Templates for rapid Customer Service response. Pricing flexibility with customer/category or product/quantity/revenue based options. Credit limit controls. Product/Batch wise or customer wise profitability. Incentive schemes in case of marketing schemes, etc. Exports and Export Documentation.
Purchase
Vendor approval mechanism, Vendor Contract pricing and tracking. Imports, Rejection tracking and Vendor assessment on various parameters
Inventory
Comprehensive and effective Inventory Management. Quarantined, Rejected, Re-workable stocks control. Consistent and coherent Lot Tracking System with product recall and explosion capabilities. Lot Attributes – Internal lot no, supplier lot no, receipt date, quarantine date, QC results. Batch tracking including expiry, destruction or renewal of expired stocks. Numerous Lot Picking Strategies.